Cet article aborde de façon synthétique et spécifique, la famille des centrales électronucléaires, utilisant la technologie des Réacteurs à Eau sous Pression. Après une présentation des principes fondamentaux de ces réacteurs, sera détaillée l’évolution vers les réacteurs dits « EPR » (« European Pressurized Reactor »).
Introduction
1. Définition et contexte
L’énergie nucléaire, après la découverte de la radioactivité (en 1896 par Henri Becquerel), puis une phase de multiples développements scientifiques et techniques (première moitié du 20ème siècle), a été utilisée depuis le milieu du siècle dernier, dans de nombreuses applications. L’une d’elles est la production d’électricité.
Différentes technologies de centrales électronucléaires ont vu le jour depuis les années 1940. Parmi elles, celle des Réacteurs à Eau sous Pression (qui seront désignées dans la suite par l’acronyme « REP ») a connu un développement important, qui fait d’elle la technologie la plus répandue au niveau mondial. Elle a fait ensuite l’objet d’une évolution vers les réacteurs dits « EPR » (« European Pressurized Reactor »).
Générations et filières successives des réacteurs électronucléaires
GÉNÉRATION ET FILIÈRE : DEUX NOTIONS DISTINCTES : Dans l’industrie nucléaire, la notion de « Génération » est distincte de celle des « Filières technologiques ». En effet, une génération peut inclure différentes technologies de réacteurs(ou filières – distinguant les différentes familles de conception / fonctionnement). Les générations successives correspondent à des critères d’exigences spécifiques à chaque période (en termes de sûreté nucléaire et au niveau de leur caractéristiques technico-économiques- construction / exploitation).
QUATRE GÉNÉRATIONS DE RÉACTEURS NUCLÉAIRES : les professionnels distinguent 4 générations de réacteurs à fission nucléaire (et non à fusion, qui est un tout autre principe physique). Chaque génération répond à des objectifs liés aux enjeux majeurs de l’époque de leur conception. Compte tenu de la durée de vie de ces équipements, on trouve encore en activité ou en cours de construction, des réacteurs de différentes générations.
- La 1ère génération de réacteurs nucléaires comprend les prototypes et les premiers réacteurs de tailles industrielles à usage commercial mis au point dans les années 1950 et 1960 et entrés en service à la fin de la décennie 1960 puis début 1970. Conçus dans l’immédiat après-guerre 1939-1945, ces réacteurs devaient faire la démonstration du potentiel de la puissance atomique mise au service de l’énergie civile et électrique. Durant cette période, la France, qui ne disposait pas des technologies d’enrichissement de l’uranium, a développé une filière technologique utilisant l’uranium naturel comme combustible (UNGG). Ce fut aussi le cas en Grande Bretagne et dans une moindre mesure en Russie.
- Les réacteurs nucléaires de 2egénération sont entrés en service à partir des années 1970, puis sur la décennie 1980. Ils correspondaient à la nécessité d’une meilleure compétitivité de l’énergie nucléaire et d’une amélioration de l’indépendance énergétique, dans un contexte de fortes tensions sur le cours des énergies fossiles (choc pétrolier). Cette étape se base également sur la mise au point d’usines civiles du cycle des matières nucléaires (enrichissement et traitement-recyclage). La majorité des réacteurs actuellement en exploitation dans le monde sont des réacteurs de génération 2. En France, il s’agit principalement de filière à eau sous pression, une technologie américaine progressivement adaptée par EDF. Des prototypes de réacteurs à neutrons rapides (RNR) ont également été construits en France sur cette période, mais le ralentissement du développement du nucléaire dans les années 1980, ajouté à la découverte de nouveaux gisements d’uranium, les ont rendus moins prioritaires.
- La 3e génération de réacteurs nucléaires, qui s’apprête aujourd’hui à prendre progressivement le relais, met l’accent sur les impératifs liés à la sûreté et à la sécurité (résistance renforcée aux agressions externes et internes – capacité à retenir les effets d’une fusion de cœur). Ces réacteurs tirent les enseignements du retour d’expérience de l’exploitation des réacteurs de génération 2. Plusieurs réacteurs répondent à ces critères : l’EPR français de 1 600 MWe, l’AP1000 (advanced pressurized de 1 000 MWe) – américano-japonais, l’AES 2006 – dernier modèle de 1 200 MWe du VVER russe, le Hualong One chinois de 1 100 MWe et l’APR 1 400 coréen de 1 400 MWe)
- La 4e génération correspond aux réacteurs, actuellement en conception, qui pourraient voir un déploiement industriel dans la seconde moitié du XXIe siècle. Ils reposent sur plusieurs concepts techniques différents : famille de réacteurs à neutrons dits « rapides », famille de réacteurs fonctionnant à plus haute température(caloporteurs gaz) ainsi que la famille de réacteurs dits « à sels fondus ».Les quatre critères améliorés auxquels ils devront répondre sont : la durabilité (optimisation de l’utilisation du combustible nucléaire pour minimiser l’utilisation de ressources naturelles et réduire les volumes / radiotoxicité des déchets), la sûreté (favoriser les dispositifs de protection passifs), la compétitivité économique (améliorer le rendement et utiliser la chaleur en plus de la production électrique), de même que la résistance à la prolifération nucléaire (en raison d’unités plus petites, parfois délocalisées).
Qu’est-ce qu’un réacteur à eau sous pression (filière REP) ?
La Partie 1 ci-dessous, détaillera le principe de fonctionnement des centrales REP. En un premier résumé rapide, le fonctionnement des REP repose sur trois circuits indépendants et successifs d’eau/vapeur, reliés par des échangeurs de chaleur pour les circuits primaire et secondaire, ainsi que par un condenseur pour les circuits secondaire et de refroidissement. La qualification de la filière REP vient de la caractéristique que le circuit primaire – comprenant le réacteur – fonctionne rempli d’eau maintenue sous forte pression pour rester liquide à haute température. Par ailleurs, l’eau agit aussi comme modérateur : c’est-à-dire qu’elle ralentit les neutrons issus des réactions de fission nucléaire (d’environ 20 000 km/seconde à 2 km/seconde), de façon à faciliter les fissions successives, nécessaires à entretenir la réaction en chaîne, qui génère la chaleur utile à produire de la vapeur d’eau, puis de l’électricité. Les REP sont dits « réacteurs à neutrons lents » et à « eau légère ou eau ordinaire ».
Brève histoire et développement des REP puis genèse du modèle EPR français – historique et constitution du parc français.
Le principe de fonctionnement REP a été élaboré au milieu du siècle dernier aux Etats Unis d’Amérique. La Société Westinghouse l’a développé et mis en œuvre dans de premières constructions aux USA.
En France, l’usage civil de l’énergie nucléaire pour produire de l’électricité a été mis en œuvre à partir des années 1950, en utilisant une autre filière : Uranium Naturel Graphite Gaz, dite « UNGG ». Comme son nom l’indique, ce type de réacteurs utilisent directement l’uranium naturel (99.3 % d’isotope non fissile U238 et 0.7 % d’isotope fissile U235) comme combustible, ainsi qu’un circuit primaire contenant du dioxyde de carbone (ou gaz carbonique), qui transporte la chaleur produite. Le modérateur est un empilement de graphite, dans lequel sont insérés de nombreux canaux avec les cartouches d’uranium combustible, développé par le Commissariat à l’Energie Atomique (C.E.A.). En tout, 6 réacteurs UNGG seront construits, de puissances grandissantes, entre 63 MW et 500 MW électriques. Ils seront arrêtés progressivement au bout d’une vingtaine d’années d’exploitation pour les plus puissants, dont le dernier à Saint-Laurent A en 1992.
Une première tranche REP sera construite en France : Chooz A dans les Ardennes, entre 1962 et 1967. C’est un modèle réduit des centrales actuelles avec une puissance électrique de 305 mégawatts. A la fin des années 1960, l’Etat Français et l’exploitant Electricité de France – E.D.F., choisissent d’adopter pour des raisons économiques et industrielles, la filière REP, en lieu et place de la filière UNGG. La construction du parc électronucléaire de REP lancé au début des années 1970, en réponse notamment aux deux chocs pétroliers, le sera sous licence « Westinghouse ». Les tranches seront progressivement « francisées », jusqu’à être totalement de technologie française, pour les 4 derniers réacteurs REP, dit « pallier N4 ». Voici l’état des constructions réalisées en France et leurs localisations en Figure 2:
- 34 réacteurs REP de 900 MW électriques (paliers successifs dits CPO, CP1 et CP2), dont les 2 réacteurs de Fessenheim en Alsace, depuis arrêtés, et non représentés ci-dessous.
- 20 réacteurs REP de 1 300 MW électriques (paliers successifs dits P4 et P’4)
- 4 réacteurs REP de 1 450 MW électriques (palier N4)
- 1 réacteur REP de 1 600 MW électriques (palier EPR)
Pour le cas spécifique de l’EPR, celui-ci utilise lui aussi le principe REP de l’eau sous pression pour le circuit primaire. Il est le fruit d’une collaboration technique entre la France (constructeur FRAMATOME) et l’Allemagne (SIEMENS KWU). Il est doté d’une puissance électrique nette de l’ordre de 1600 MW électriques, intègre les équipements des paliers N4 français et KONVOI allemand, ainsi que des dispositifs de sûreté nucléaire, issus du REX des accidents de Three Mile Island aux USA en 1979 et de Tchernobyl en Ukraine en 1986.
Importance de la production électrique d’origine nucléaire en France, en 2023.
Voici la répartition de la production d’électricité en France pour 2023 par origine (Figure 3). L’électricité n’existe pas d’elle-même dans le milieu naturel, elle est dite « énergie finale », issue de la transformation d’ « énergies primaires », représentées ci-dessous (Nota : 1 Téra watt heure = 1 TWh = 1 milliard de kWh (kilo watt heure)
Au niveau mondial, en 2023, environ 407 réacteurs nucléaires sont en fonctionnement (ainsi que 62 en construction), toutes filières confondues (REP et autres technologies).
Partie 1 : Principe de fonctionnement REP
1. Structure de base d’un REP
Schéma simplifié d’un réacteur REP
Voici le schéma simplifié d’un réacteur REP, composé de trois circuits indépendants principaux :
Nota : le schéma ci-dessus représente une tranche nucléaire comportant un circuit de refroidissement dit « ouvert », pour un site en bord de mer. Certaines tranches en bord de rivière, sont dotées d’un circuit « fermé », la majorité de l’eau étant alors refroidie par un aéroréfrigérant atmosphérique : tour creuse en béton entre 160 et 200 mètres de haut, créant un courant d’air naturel. Le panache présent au-dessus de ces tours est composé uniquement de vapeur d’eau.
Description du principe de fonctionnement avec les composants principaux (cuve du réacteur, générateurs de vapeur, pompes, turbines à vapeur, alternateur)
Le principe de fonctionnement d’une tranche REP, repose sur la production de grandes quantités de chaleur, produites dans le circuit primaire (logé dans l’enceinte de confinement du bâtiment réacteur (« Zone ou Ilot Nucléaire »). La cuve du réacteur contient des assemblages de combustible à base d’uranium enrichi, dans lesquels se produit une réaction de fission nucléaire contrôlée. Le circuit primaire contient de l’eau ordinaire maintenu sous forme liquide (à environ 320 °C sous 155 bars de pression – c’est-à-dire environ 155 fois plus que la pression atmosphérique), grâce au pressuriseur. La chaleur transportée, est amenée à plusieurs générateurs de vapeur (3 ou 4 par tranche en fonction de leur puissance), qui porte à ébullition l’eau du circuit secondaire. L’eau est mise en circulation par autant de puissants groupes motopompes primaires (dites « GMPP »).
La vapeur d’eau ainsi produite est conduite vers le groupe turbo-alternateur (dit « GTA »), situé en salle des machines (bâtiment non nucléaire, ou « Ilot Conventionnel »). Là, plusieurs étages de turbines à vapeur convertissent l’énergie thermodynamique du flux de vapeur, en énergie cinétique puis en couple mécanique, entraînant la rotation à 1500 tours par minute de la ligne d’arbre. En bout de cet axe se situe un alternateur permettant de produire l’électricité (sous une fréquence de 50 Hz et une tension de 20 à 23 kV, qui sera ensuite portée à 400 kV par le transformateur principal, lui-même connecté au réseau électrique national de transport).
La vapeur détendue est ensuite envoyée dans un très large condenseur, dont le rôle est de la retransformer en eau liquide, afin de la ré-envoyer, au moyen de pompes, vers les générateurs de vapeur, afin de recommencer un nouveau cycle. L’eau du circuit de refroidissement (environ 50 à 60 m3 / seconde) est prélevée et restituée au milieu naturel, avec un échauffement contrôlé. Il s’agit de l’eau du milieu marin, ou d’un grand fleuve. Lorsque le débit de cette source froide est limité (rivière plus petite), un circuit fermé, doté d’une tour aéroréfrigérante atmosphérique permet de ne prélever qu’environ 2 m3 / seconde et par tranche.
Caractéristiques principales, chaîne de conversion de l’énergie, rendement, dimensionnements
Voici un tableau récapitulatif des principales données chiffrées du pallier EPR Flamanville 3 (1600 MWe), en regard du REP français N4 (1450 MWe) :
|
UNITE | PALLIER EPR | PALLIER N4 |
GENERALITES | |||
Puissance thermique du cœur | MWth | 4500 | 4250 |
Puissance électrique nette vers le réseau électrique |
MWe |
1600 |
1450 |
CONCEPTION DU CŒUR | |||
Nombre d’assemblages | Nombre | 241 | 205 |
Instrumentation cœur | Mesure de flux neutronique en 3D permanente. Montage sur le couvercle de cuve (fond de cuve lisse) : 40 aéroballs, 72 détecteurs de neutrons, 36 thermocouples sortie coeur | Montage par le bas de cuve, 6 détecteurs neutrons mobiles, 52 thermocouples sortie cœur | |
Débit GMPP – Moto-Pompes Primaires | m3/heure | 28 330 | 24 850 |
Refroidissement réacteur à l’arrêt – RRA | 4 pompes hors enceinte | 2 pompes dans l’enceinte | |
Injection de Sureté Basse Pression – RIS BP | 4 pompes | 2 pompes | |
Borication de secours – RBS | 2 trains RBS spécifiques | Utilisation RCV | |
ALIMENTATION GV | |||
Au démarrage | Système dédié AAD (1 pompe) | Utilisation ASG | |
En situation accidentelle | 4 trains ASG séparés | 2 motopompes et 2 turbopompes | |
Refroidissement PTR | 2 trains principaux et 1 train de secours | 2 trains (1 pompe par train) | |
REFROIDISSEMENT RRI (refroidissement auxiliaires nucléaires) | 4 trains | 2 trains | |
SYSTEMES ELECTRIQUES | 4 trains indépendants en 4 divisions | 2 trains indépendants en 2 divisions | |
Salle de commande | Informatisée | Informatisée | |
Alimentation de secours | Concept 4 trains, 4 divisions avec 4 diésels de 7 MW dans des bâtiments séparés et 2 diésels d’ultime secours | Concept 2 trains dans 2 divisions, avec 2 diésels de 8 MW, dans des locaux séparés, 1 turbine LLS de 135 kW et 1 TAC de 7 MW, 1 Diésel Ultime Secours 3 MW | |
ENCEINTE DE CONFINEMENT | 2 enceintes béton, avec une peau interne d’acier | 2 enceintes béton | |
Volume de l’enceinte | m3 | 80 000 | 72 700 |
Bâche PTR | Dans l’enceinte | Hors enceinte | |
GROUPE TURBO ALTERNATEUR – GTA | Turbine type ARABELLE | Turbine type ARABELLE | |
Pression admission | bars absolus | 75.2 | 71 |
Puissance active | MW | Environ 1755 | Environ 1539 |
Vide au condenseur | milli-bars absolus | 46 | 63 |
Nota 1: le rendement d’une centrale électronucléaire reflète d’une part les contraintes liées à la thermodynamique (conversion de chaleur en électricité) et d’autre part, la consommation électrique interne, pour assurer le fonctionnement de tous les organes : pompes, autres systèmes auxiliaires, contrôle commande, etc… Ainsi pour l’EPR, de puissance de l’ordre de 1600 MW électrique nette, le rendement est dans une échelle classique du pallier REP : soit environ un tiers(par rapport à la puissance thermique du réacteur d’environ 4 500 MW thermique).
Nota 2 : les constructeurs des parties actives principales sont FRAMATOME pour la chaudière nucléaire et ARABELLE SOLUTIONS pour le groupe turbo-alternateur (précédemment successivement General Electric après ALSTOM Power). L’acronyme « ARABELLE » désigne le nom commercial de cette dernière génération de turbine à vapeur.
2. Réaction nucléaire
Explication de la fission nucléaire en chaine
Voici, illustrées en Figure 5, les principales étapes d’une réaction en chaîne de fission, s’entretenant dans les assemblages de combustible d’uranium. Elle s’accompagne d’un fort dégagement de chaleur, utilisée pour produire ensuite de la vapeur d’eau en forte quantité (animation éditée par EDF):
En résumé :
Figure 5 – Illustrations des principes de fission et réaction en chaîne nucléaire
Combustible utilisé (uranium enrichi)
Le combustible utilisé est enrichi à un peu plus de 4% en uranium 235 (pour le palier EPR). Cet enrichissement, plus élevé que sur les paliers précédents (4% environ) permettra une gestion du combustible plus souple et des cycles pouvant aller au-delà des 12 à 18 mois pour les REP hors EPR), ce qui aura un impact positif sur la disponibilité (Kd).
Cet uranium est contenu dans des assemblages combustible – Figure 6 :
Le cœur du réacteur, où se produit la réaction en chaîne, contient un ensemble d’assemblages combustibles, disposés verticalement. Chaque assemblage contient 264 crayons combustibles, tubes en alliage de zirconium dans lesquels sont empilées des pastilles d’uranium enrichi de 8 mm de diamètre et 13 mm d’épaisseur. La hauteur des crayons et donc des assemblages, varie selon la puissance du réacteur (de 4 m à 4,80 m), tout comme le nombre d’assemblages insérés dans le cœur (de 157 pour un réacteur de 900 MWe à 205 pour un réacteur de 1 300 MWe, ou encore 241 pour un EPR de 1 600 MWe). Chaque assemblage combustible a une section carrée de 20 centimètres de côté et pèse entre 500 et 800 kilogrammes.
La structure de l’assemblage comporte 25 tubes-guides dans lesquels coulissent les crayons absorbants des grappes de commande, tenus par une « araignée », pièce métallique dont les déplacements vers le haut ou vers le bas permettent de faire monter ou descendre la grappe.
Principes de sûreté nucléaire – les trois règles fondamentales
Le maintien PERMANENT des trois fonctions de sûreté suivantes est primordial pour assurer le fonctionnement du réacteur (y compris lors des arrêts, cœur déchargé en piscine combustible):
- le contrôle de la réaction en chaîne est assuré par l’absorption plus ou moins importante des neutrons. Pour cela deux moyens : tout d’abord les grappes de commande (ou barres de contrôle) sont insérées plus ou moins profondément dans le cœur du réacteur puis la concentration en bore (produit neutrophage), dans l’eau du circuit primaire, est plus ou moins importante.
L’insertion complète des grappes de commande dans la cuve provoque l’arrêt quasi immédiat de la réaction en chaîne. Leur chute (en 2 secondes) peut être obtenue par gravité, en cas d’absence d’alimentation électrique. Cette capacité de chute libre est testée avant chaque redémarrage.
En parallèle, l’ajustement de la concentration de l’eau en bore permet de compenser « l’usure » du combustible : cette dernière est réduite progressivement tout au long du cycle de production (qui dure entre 12 et 18 mois).
- le refroidissement du combustible peut être assuré par les générateurs de vapeur (en fonctionnement, en transitoires de démarrage arrêt, et à l’arrêt) ou par le circuit de refroidissement RRA (refroidissement réacteur à l’arrêt). Pour ne pas endommager les assemblages et les gaines des crayons, la chaleur dégagée dans ces crayons doit être évacuée en continu. En cas d’arrêt du réacteur, il s’agit aussi d’évacuer la chaleur résiduelle qui subsiste après l’arrêt de la réaction en chaîne principale (quelques % de la puissance thermique nominale). En situation accidentelle, le refroidissement est assuré par les systèmes d’injection de sécurité.
- le confinement de la radioactivité permet d’éviter la dispersion des produits radioactifs dans l’environnement. Il est assuré par les trois barrières successives que sont les gaines du combustible, l’enveloppe métallique du circuit primaire et l’enceinte de confinement du bâtiment réacteur.
Partie 2 : Principaux circuits
1. Circuit primaire
Fonctionnement du circuit primaire :
Le circuit primaire est contenu dans le bâtiment cylindrique du bâtiment réacteur (Figure 8). A noter que de nombreux systèmes auxiliaires (pour le fonctionnement normal mais aussi pour assurer les fonctions de sûreté, sont présents dans plusieurs bâtiments mitoyens). Afin de simplifier nous ne présenterons ici que le circuit primaire lui-même.
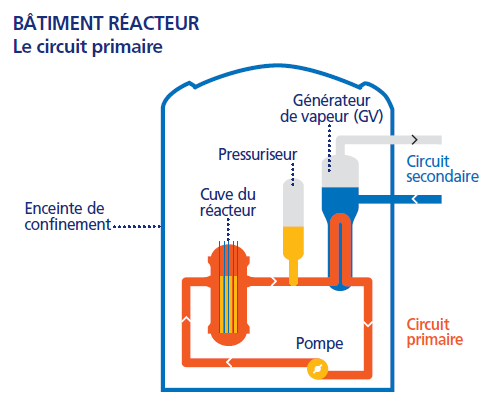
Le bâtiment réacteur, cylindrique, est constitué d’une paroi en béton qui tient le rôle d’enceinte de confinement, essentiel pour la sûreté, la radioprotection et la protection de l’environnement.
Le circuit primaire (fermé) assure, via les générateurs de vapeur, la transmission de la chaleur dégagée dans le cœur du réacteur à l’eau du circuit secondaire. Il comprend, en fonction du palier de puissance, 3 ou 4 boucles identiques, mais en relation directe entre elles (pas de vannes sur le circuit primaire) comprenant :
- une seule cuve – Figure 9,
- 3 ou 4 générateurs de vapeur (échangeurs de chaleur placés entre le circuit primaire et le circuit secondaire),
- 3 ou 4 pompes primaires qui assurent la circulation de l’eau du circuit primaire,
- un seul pressuriseur, dont le rôle est de maintenir l’eau du circuit primaire sous forte pression (155 bars) pour éviter l’ébullition de l’eau, portée à environ 320°C.
NB : Le schéma est représenté avec un seul générateur de vapeur (GV).
Cœur du réacteur – contrôle de la réaction en chaîne :
Le cœur du réacteur est composé d’assemblages combustibles d’uranium, refroidis par l’eau du circuit primaire. Lors de la fission nucléaire, un neutron est projeté sur un atome d’uranium, le noyau. En se cassant, celui-ci libère de l’énergie calorifique, des rayonnements ionisants et deux ou trois neutrons qui vont à leur tour frapper d’autres noyaux. C’est la « réaction en chaîne » qui produit la chaleur intense nécessaire à la production d’un flux important de vapeur d’eau envoyée ensuite vers la turbine de la salle des machines.
En fonctionnement normal, la cuve du réacteur est remplie d’eau restant sur forme liquide. Maintenue à une pression de 155 bars, elle sort du réacteur à une température d’environ 320° C.
Les grappes de commande, insérées plus ou moins profondément dans le cœur du réacteur, permettent de contrôler la réaction en chaîne (réglage de la puissance fournie) ou de la stopper (arrêt du réacteur par chute des grappes).Les tubes des grappes, en inox, sont remplis d’un alliage dont la composition est généralement de 80 % d’argent, 15 % d’indium, et 5 % de cadmium, matériau absorbant les neutrons. Dans les faits, il existe plusieurs types de grappes de commande, permettant de remplir différentes fonctions de contrôle du cœur.
Comme déjà évoqué précédemment, un autre moyen de contrôle de la réactivité (intensité de la réaction en chaîne), de façon en particulier à compenser l’usure progressive du combustible, consiste à dissoudre, ou à retirer dans/de l’eau du circuit primaire une quantité contrôlée d’acide borique (substance qui elle aussi absorbe les neutrons).
Le pilotage du réacteur se fait en contrôlant en permanence la température et la pression du circuit primaire, qui doit rester dans un domaine de fonctionnement prédéfini. Il est représenté de façon simplifiée ci-dessous. Ce diagramme (Figure 10), est appelé la « Chaussette » du régime de fonctionnement à respecter pour rester dans le domaine garantissant la sûreté nucléaire.
2. Circuit secondaire
Conversion de la chaleur en vapeur :
Le circuit secondaire(ou circuit eau-vapeur en Figure 11), fermé, apporte la vapeur d’eau produite dans les générateurs de vapeur jusqu’au groupe turbo-alternateur. En faisant tourner les différents étages des turbines le composant, la vapeur cède progressivement une grande partie de son énergie. La partie restante (mélange d’eau et de vapeur) est ensuite complètement transformée en eau au contact des 92 916 tubes du condenseur (pour l’EPR). Cette eau est réinjectée dans les générateurs de vapeur, après réchauffage (utilisant des prélèvements de vapeur vive), dégazage (pour retirer tous les gaz dissous), à l’aide de puissantes pompes (turbopompes alimentaires tournant avec de la vapeur vive prélevée hors EPR, ou motopompes actionnées par des moteurs électriques dans le cas de l’EPR.
Principaux composants du circuit secondaire :
- SALLE DES MACHINES : bâtiment mesurant environ 50mètres de haut, en forme de parallélépipède.
- TURBINE : Constructeur : ALSTOM (devenu ARABELLE SOLUTIONS) Technologie ARABELLE (pour les paliers N4 et EPR), contraction de Alstom Rateau BELfort : type de turbine développée par Alstom avec les entités de Rateau à La Courneuve et Alstom Belfort. Elle est composée d’une corp haute et moyenne pression (HMP) et de trois corps basse pression (BP). Poids total : 938 tonnes. Chaque corps basse pression est composé de 615 ailettes et pèse 267 tonnes. Vitesse de rotation de la turbine en fonctionnement nominal : 1 500 tours/minute soit une vitesse circonférentielle (au niveau extérieur des aubes les plus grandes) de 2 fois la vitesse du son !Cette vitesse de rotation permet de produire une électricité en courant alternatif à 50 Hz (50 alternances du courant électrique par seconde).
- ALTERNATEUR : Constructeur : ALSTOM (devenu ARABELLE SOLUTIONS) Technologie GIGATOP (pour les paliers N4 et EPR). L’alternateur est une pièce maîtresse car c’est lui qui transforme l’énergie mécanique de rotation de l’arbre (le couple mécanique) en énergie électrique. Au centre, une partie mobile, le rotor, est entraîné par la turbine à 1 500tours/minute. ll est constitué de bobinages où circule un courant électrique continu qui crée un champ magnétique. Autour du rotor :une autre pièce constituée de bobinage reste fixe, le stator. Quand le rotor tourne à l’intérieur du stator, il se produit une variation du champ magnétique qui induit un courant dans le stator :c’est l’électricité !Ce courant électrique en sortie d’alternateur est à environ 23 000 Volts / 48 000 Ampères. Il est converti en 400 000 V / 2 700A pour pouvoir circuler sur le réseau électrique national. La très haute tension permet de diminuer les pertes par échauffement (effet joule) sur les lignes de transport. Autres caractéristiques pour une tranche EPR :
- Poids du rotor : 269 tonnes
- Poids du stator : 646 tonnes
- Poids total avec excitatrice : 937 tonnes
- Tension : 23 KV – puissance maximale 1950 MVA soit une puissance équivalente à 2 300 000 chevaux !
Le groupe turbo-alternateur mesure près de 70mètres de long soit la longueur d’un Airbus A380
- CONDENSEUR : sa fonction est d’évacuer l’énergie résiduelle de la vapeur, qui n’est plus utilisable, vers le milieu extérieur, en retransformant la vapeur détendue en eau liquide. Caractéristiques principales pour une tranche EPR :
- 40 mètres de long
- 20 mètres de large
- 92 916 tubes parcourus par de l’eau de mer. Mis bout à bout, cela représente 1470km soit la distance Flamanville – Vienne en Autriche.
- La surface d’échange est de : 85811 mètres carrés.
- Volume total du condenseur : 7586 mètres cube : c’est la plus grande capacité en eau de l’installation.
- Poids total : 2450 Tonnes.
- Débit d’eau de refroidissement : environ 60 m3 / seconde
- GROUPES SÉCHEURS-SURCHAUFFEURS (2 équipements) : ils ont pour fonction de séparer mécaniquement l’eau de la vapeur en provenance de la turbine haute pression et assurent la surchauffe de cette vapeur à l’aide d’échangeurs, avant de l’envoyer vers la turbine moyenne pression. Contrairement aux paliers précédents, les groupes sécheurs surchauffeurs sur l’EPR sont implantés de façon verticale. Caractéristiques principales pour une tranche EPR :
- Poids unitaire : 406 tonnes
- 5,8 mètres de diamètre
- 23 mètres de hauteur
3. Circuit de refroidissement marin ou atmosphérique
Principales caractéristiques pour un site en bord de mer, en circuit ouvert :
Dans le cas d’une installation en bord de mer, comme pour l’EPR Flamanville 3, l’eau utilisée dans le circuit de refroidissement est directement collectée en mer via un canal d’amenée, au niveau de la station de pompage. Le volume de circulation nominal est d’environ 60 mètres cube par seconde. Une fois utilisée pour refroidir les matériels de l’installation (circuit de refroidissement),elle est rejetée au niveau de l’ouvrage de rejet (Figure 12), puis empreinte un tunnel de 700mètres, et est rejetée au large (pour ne pas recirculer via le canal d’amenée), via un large diffuseur, de façon à diluer largement les volumes et diminuer les hausses locales de température. Ce tunnel de 5 mètres de diamètre a été creusé par un tunnelier à 50 mètres de profondeur pour permettre le rejet de l’eau de refroidissement en mer. Un arrêté de rejet réglemente la température de rejet de l’eau en mer pour ne pas impacter l’environnement marin : la différence de température entre le pompage dans le canal d’amené et son rejet en mer ne doit pas dépasser les 14°C. En moyenne, l’eau est rejetée à + 6 à + 8°C(Cette température est mesurée à la sortie du diffuseur).Quasiment 100 % des volumes d’eau prélevés en bord de mer pour le refroidissement sont restitués quelques minutes plus tard au milieu naturel.

Nota : les rejets CRF et SEN se font indifféremment des 2 côtés du déversoir
Principales caractéristiques pour un site en bord de rivière en circuit fermé :
Lorsque le débit de cette source froide est limité (rivière plus petite), un circuit fermé, doté d’une tour aéroréfrigérante atmosphérique(Figure 13) permet de ne prélever qu’environ 2 m3 / seconde et par tranche. L’évacuation de la chaleur se fait via un panachage exclusivement constitué de vapeur d’eau (environ 0,5 à 0,7 mètres cube par seconde et par tranche), le reste du volume prélevé est restitué à la rivière et sert à éviter une accumulation de sédiments dans le bassin de l’aéroréfrigérant.
Partie 3 : Evolutions du pallier REP vers le modèle EPR , Sûreté et Innovations
1. Dimensionnements
Genèse franco-allemande du design EPR:
Un réacteur à eau pressurisée de type EPR a une puissance électrique nette pour le réseau d’environ 1 600 MWe. Il intègre nombre de progrès récents en matière de sûreté, de réduction d’impact environnemental et de performance technique et économique pour fournir une électricité sûre, compétitive et bas carbone. Les choix de conception de la chaudière sont issus, pour la plupart, du REX du palier N4 français (constructeur FRAMATOME / AREVA NP) et des réacteurs allemands de type KONVOI (constructeur SIEMENS KWU).
2. Dispositifs de sûreté supplémentaires
Systèmes de sûreté passifs et actifs :
- La coque « avion » – Figure 14 : Le réacteur EPR bénéficie d’une protection de l’îlot nucléaire accrue contre les actes intentionnels de malveillance, y compris la possibilité d’une chute d’avion de ligne gros porteur sur le site.
- Le récupérateur de corium et le réservoir d’eau IRWST, interne au bâtiment réacteur – Figure 15 : le réacteur EPR bénéficie d’une réserve d’eau au plus près du réacteur et d’un dispositif conçu pour contenir et refroidir le cœur du réacteur en situation accidentelle (fusion du cœur).
Redondance et résilience des systèmes :
- Quatre systèmes de sauvegarde 100 % indépendants – Figure 16.Ils garantissent une quadruple redondance au niveau de leurs composants électriques et mécaniques, comme sur le plan de leurs systèmes de contrôle-commande. Chaque train peut ainsi assurer à lui seul l’ensemble des fonctions de sûreté du réacteur. Cette configuration permet d’envisager de réaliser une partie de la maintenance tranche en marche.
- La salle de commande informatisée :
Le réacteur EPR bénéficie d’un moyen de conduite principal informatisé. Le système de contrôle-commande permet aux opérateurs de contrôler et de piloter l’ensemble du réacteur. Doté des technologies numériques les plus récentes, ce système centralise toutes les données d’exploitation. La plateforme logicielle est un standard de FRAMATOME (TELEPERM). De même que pour le pallier N4, une salle de commande informatisée (Figure 17) permet aux opérateurs d’assurer la conduite de l’installation.
Un moyen de conduite de secours est aussi disponible utilisant des interfaces de commandes non informatisées. Ceci constitue un moyen technologiquement diversifié, pour éviter les indisponibilités de mode commun.
3. Innovations technologiques – avancées par rapport aux réacteurs de générations précédentes
Spécificités de l’Instrumentation Cœur Réacteur « Système RIC »:
Cette instrumentation permettant de suivre les paramètres essentiels du cœur composé des 241 assemblages combustible :
- amplitude et répartition du flux de neutrons (équivalent au compte tours moteur d’une voiture),
- températures cœur et dôme du réacteur
- niveau d’eau en regard des tubulures de la cuve : mesure essentielle pour estimer la couverture en eau du cœur, un des paramètres fondamentaux de sûreté nucléaire.
L’instrumentation cœur de l’EPR est héritée du design des centrales allemandes KONVOI. Elle accède au cœur totalement par le couvercle de la cuve (situé donc en partie haute). Ceci fait que le fond de la cuve du réacteur EPR n’a aucune traversée (à la différence des autres réacteurs du parc français), ce qui constitue un avantage pour faciliter l’auscultation de la cuve lors des arrêts de tranche et un gain de sûreté, le fond de cuve étant uniforme.
Cette instrumentation cœur est constituée de 2 dispositifs principaux, propres au palier EPR – Figure 18 :
- mesure en continu du flux neutronique et de la température dans le cœur par les « collectrons » (capteurs au cobalt, générant un courant électrique proportionnel à l’intensité du flux de neutrons, aussi dénommés « SPND » Self Powered Neutron Detectors) et thermocouples température.
- mesure cyclique, donc non continue, de l’amplitude et répartition du flux de neutrons par un système de billes de vanadium, introduites et retirées du cœur par un système pneumatique sous azote : ce système permet de dresser une carte de répartition du flux neutronique, par mesure du rayonnement des billes sur une table hors cuve, proportionnel à l’intensité du flux traversé. Ce système est dénommé AEROBALLS MESUREMENT SYSTEM (ou AMS).
Les systèmes de sauvegarde, dont certains ont une configuration spécifique pour EPR:
-RBS -Borication de Sécurité du Réacteur : automatique ou manuelle du circuit primaire, quel que soit le niveau de la pression dans le CPP. Il permet d’atteindre un état contrôlé ou un état sûr. Il doit également permettre l’isolement des soutirages du circuit primaire à la suite d’un signal d’injection de sécurité, afin de garantir son efficacité pour le maintien de l’inventaire en eau.
– RIS/RA : La fonction RIS/RA réunit 2 fonctions distinctes hors EPR : le mode RA (Refroidissement du réacteur à l’Arrêt) et le mode IS (Injection de Sécurité) constitué du RISBP (Injection de Sécurité Basse Pression commune avec la partie RA), du RISMP et des accumulateurs, mais pas de RISHP sur l’EPR.
-EVU – Evacuation Ultime de puissance : assurer le transfert de la chaleur résiduelle de l’IRWST vers l’EVU intermédiaire lui-même refroidi par la source froide ultime (SRU) lors d’évènements RRC-A ou PCC-4(cf. §30), assurer le transfert de chaleur de l’enceinte vers l’IRWST par l’aspersion AG(Accident Grave), réaliser un noyage passif de la zone d’étalement du corium et l’isolation thermique du radier en cas de fusion du cœur. Ce circuit permet également de refroidir la3ème file PTR.
– ASG : Alimentation de Secours des Générateurs de Vapeur. Contrairement aux autres paliers, ce circuit est dédié exclusivement à la sauvegarde.
-VDA : Circuit de Décharge de la Vapeur à l’Atmosphère dédié à la sauvegarde
– SRU : Circuit qui répond au besoin de créer une source froide diversifiée venant pallier la défaillance de la source froide du site.
Les circuits annexes spécifiques à l’EPR:
-IRWST : Bien que n’étant pas un circuit en lui-même (il appartient au RIS), le réservoir d’eau borée (bâche PTR sur les autres paliers) d’un volume de 2000 m3 est situé à l’intérieur du bâtiment réacteur.
-TEP – Dégazage et Traitement en continu de l’Eau du circuit Primaire de process et stockage de l’eau déminéralisée pour REA.
-TEG -Traitement des Effluents Gazeux, recombinaison H2/O2 et décroissance des gaz actifs. La technologie utilisée pour la collecte et le traitement des gaz actifs est tirée de la technologie allemande KONVOÏ et fonctionne en circuit fermé.
-AAD – Ensemble motopompe Alimentaire d’Arrêt et de Démarrage : pour que le système ASG soit dédié exclusivement à la sauvegarde, l’alimentation des GV en phase de démarrage/arrêt est effectuée par une seule pompe AAD non secourue électriquement, mais secourue par l’ensemble motopompe alimentaire APA – Ensemble motopompe alimentaire. L’injection est réalisée via une vanne très petit débit ARE – Alimentation normale en eau des générateurs de vapeur.
Ces dispositifs, en plus de disposer de 6 diésels principaux, regroupés dans 2 bâtiments distincts, parasismiques et protégés des inondations ont permis que le design EPR n’a pas eu besoin de modifications majeures à la suite du réexamen de sûreté mené en 2011 et 2012 en France, à la suite de l’accident de Fukushima. En effet, les principaux dispositifs préconisés avaient déjà été intégrés à la conception initiale générique de l’EPR, avant même cet accident. En effet, l’EPR été déjà doté des diésels de secours supplémentaires, avec des technologies diversifiées (pour éviter les pannes de mode commun), de bâtiments résistants aux séismes (et chute d’avion), des protections contre les inondations, etc… Seules de revues spécifiques au site ont été entreprises (dont tenue sismique des canalisations depuis les bassins d’eau douce en haut de falaise, connexions directes en eau et électricité depuis l’extérieur de l’îlot nucléaire).
Conclusion -Résumé des points clés :
Points essentiels du design EPR – Robustesse du design
Les chapitres précédents ont pu détailler les principes de renforcement de la sûreté nucléaire du design EPR intégrés dès sa conception, ayant eu lieu lors de la première décennie 2 000. Ceux-ci permettent de classer l’EPR en Génération 3.
La pertinence de ces améliorations a pu s’illustrer lors des réexamens de sûreté à la suite de l’accident de la centrale de Fukushima au Japon en mars 2011. Ces études se sont déroulées sur les années 2011-2012 pour le Parc EDF. Les principes retenus ont été de renforcer la résilience des moyens de secours d’alimentation en eau et en électricité, résistance aux séismes, aux inondations, ainsi que la faculté d’intervenir sur plusieurs tranches potentiellement accidentées en parallèle. Là où sur le parc des réacteurs génération 2 ont été installés plusieurs dispositifs supplémentaires (dont les Diésels d’Ultime Secours (DUS), les connexions externes électriques et d’eau d’ultime secours), il n’y a pas eu besoin de modifier le design de l’EPR (ou seulement à la marge), qui avait intégré ces équipements dès sa conception avant même l’accident de Fukushima.
D’autres dispositifs ont été intégrés pour optimiser les aspects technico-économiques d’exploitation, tels que le concept « Two-rooms » du bâtiment réacteur, qui permet de le sectoriser par des portes neutroniques et de permettre l’accès à une zone de service pour anticiper des travaux de maintenance même réacteur en puissance,
Mise en service en cours de FLA3 – Premiers éléments de REX – Retour d’Expérience des 3 autres EPR en service : « EPR Family »
L’EPR de Flamanville 3 est en cours de démarrage, à la suite de l’autorisation de mise en service délivrée par l’Autorité de Sûreté Nucléaire du 7 mai 2024. A l’heure où cet article est produit, le combustible a été chargé en réacteur et la première divergence a eu lieu le 3 septembre 2024. C’est ainsi le 4ème EPR à entrer progressivement en exploitation, après les deux EPR de TAISHAN en Chine (connections au réseau électrique respectivement en juin 2018 et juillet 2019) et l’EPR d’Olkiluoto 3 (connecté en mars 2022), vue ci-dessous Figure 19:
Ces mises en services successives permettent de constituer un REX utile au démarrage de Flamanville 3, qui pourra ensuite être pris en compte pour les autres tranches nucléaires.
Les EPR en service montrent des performances de production très intéressantes, à l’image du réacteur TAISHAN 2, qui détient le record de la production électrique annuelle la plus importante, avec une production de 12,8 TWh en 2023.
Développements actuels et futurs à l’export
L’industrie nucléaire française a historiquement développé son activité à l’international. A l’image de la collaboration franco-chinoise des années 1990, avec la construction de 2 unités 900 MWe à Daya Bay et Ling Ao, puis les EPR de TAISHAN dans la décennie 2010 – Figure 20, cet élan se poursuit au sud-ouest de la Grande Bretagne, avec les deux EPR en construction à HINKLEY POINT C – Figure 21.
Ce programme devrait s’amplifier avec le projet de réplication pour deux EPR supplémentaires sur la côte ouest de l’Angleterre, sur le site de SIZEWELL C. Vue d’artiste du projet en Figure 22 :
Evolutions à venir vers le palier EPR 2
Cette première série de 4 EPR en service, 2 tranches en construction en Grande Bretagne, ainsi qu’un projet de 2 supplémentaires a fait l’objet d’une revue approfondie afin d’industrialiser la construction de futurs EPR : il s’agit du programme « EPR2 ». Plusieurs objectifs ont été pris en compte : rationaliser le design, tout en conservant le même degré de sûreté nucléaire afin de réduire les coûts unitaires et les durées de construction.
Plusieurs choix ont été retenus, parmi lesquels : réduire à 3 le nombre de trains 100 % d’auxiliaires nucléaires, enceinte de confinement unique (tout en conservant le principe de la « coque avion »), réduction/standardisation du catalogue des matériels utilisés (pompes, robinetteries), usage de la préfabrication en usine de certains sous-ensembles, construction par paires de tranche.
Au-delà du programme EPR2, et au niveau mondial, la production d’électricité décarbonée est essentielle pour contribuer à atteindre les objectifs de développement durable et limiter l’évolution du climat, en effet plus de 60 % de l’énergie électrique mondiale est encore produite, en 2023, par des énergies fossiles (source Statistical Review of World Energy Council, juin 2023). Les experts (AIE – Agence Internationale de l’Energie, GIEC – Groupe Intergouvernemental sur l’Evolution du Climat) s’accordent à dire que le nucléaire devrait ainsi connaitre un fort développement dans les prochaines décennies pour constituer une partie plus importante des futurs mix énergétiques. La filière nucléaire devra, pour cela, relever l’ensemble des défis technologiques, industriels et humains qui l’attendent.
Références
Liste des sources et documents consultés :
-
- EDF – avril 2019 – Infographies pour une communication sur l’électronucléaire
- EDF – Eté 2023 – EPR Flamanville 3 – Mémento visites
- EDF – juin 2021 – Référentiels de construction et caractéristiques EPR Flamanville 3
- IRSN – 2022 – Cartes des sites électronucléaires français
- Réseau de Transport d’Electricité – 2023 – Bilan électrique 2023
- CEA – 2015 – Présentation des quatre générations de réacteurs nucléaires
Lexique – abréviations anglosaxonnes citées :
- EPR : European Pressurized Reactor », parfois aussi dénommé« Evolutionary Pressurized Reactor
- SPND : Self Powered Neutron Detectors: capteur de flux neutronique, constitué de bore, générant un courant électrique proportionnel à l’intensité du flux neutronique, spécifique au design EPR.
- IRWST : In Reactor Water Storage : réservoir d’eau situé en partie basse du bâtiment réacteur, spécifique au design EPR.
Rédacteurs :
- Etienne ACKERMANN – Electricité de France
De formation ingénieur, Etienne a travaillé pendant 10 ans dans différents secteurs de l’industrie avant de rejoindre en 2012 le groupe EDF. Il a travaillé 12 ans sur le projet de construction de l’EPR de Flamanville sur des postes dans le contrôle de projet jusqu’à son dernier poste de Directeur Performances (en charge de la performance, des outils et des méthodes) jusque fin 2024.
- Philippe ESPINASSE – Electricité de France
Ingénieur chez EDF, Philippe a travaillé depuis plus de 25 ans dans les domaines des réseaux électriques et du nucléaire. Il a une expérience de plus d’une douzaine d’années dans des projets énergétiques pour et à l’export. Il a occupé différents postes au Projet Flamanville 3, dont au Groupe Chaudière Nucléaire – NSSS (Nuclear Steam Supply System).
- Guillaume SIMON – Electricité de France
Depuis plus de 15 ans, Guillaume a occupé plusieurs postes dans l’ingénierie et le pilotage de projet dans le cadre de la conception et de la construction des EPR chez EDF. Il a occupé dernièrement le poste de Directeur Technique du Projet EPR Flamanville 3